化工行业设备完整性管理与预测性维修系统是确保生产安全、高效运行的重要保障。在化工生产过程中,设备的稳定运行直接关系到生产效率、产品质量以及安全生产等多个方面。设备完整性管理强调从设备的设计、采购、安装、调试、运行到退役的全生命周期管理,通过建立完善的管理体系和标准,确保设备始终处于良好的运行状态。而预测性维修系统则是基于设备运行数据和先进的分析技术,推算设备可能出现的故障,从而合理安排维修计划,避免设备突发故障导致的生产中断和安全事故。设备完整性管理需要定期更新维护计划。安全设备完整性管理与预测性维修系统维护记录
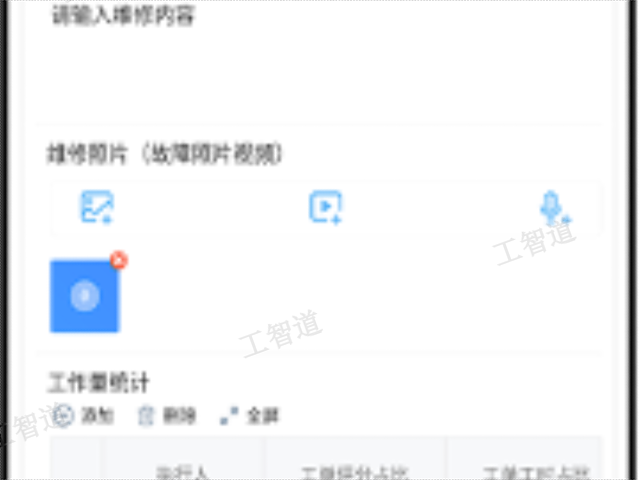
人员培训是确保设备完整性管理与预测性维修系统有效运行的重要环节。化工企业应定期组织针对设备管理人员、维修人员和操作人员的培训活动。培训内容应涵盖设备完整性管理的理念、方法和工具,预测性维修系统的操作、数据分析和故障诊断技术等方面。通过理论讲解、案例分析和实际操作相结合的方式,提升员工的专业知识和技能水平。在培训过程中,可以邀请行业专业人士和设备制造商的技术人员进行授课,分享新的技术和管理经验。同时,鼓励员工参与外部的培训和交流活动,拓宽视野,了解行业内的先进做法和发展趋势。企业还可以建立内部的知识共享平台,方便员工随时查阅培训资料和交流学习心得。系统化设备完整性管理与预测性维修系统维护系统传感器在预测性维修中起着重要作用。
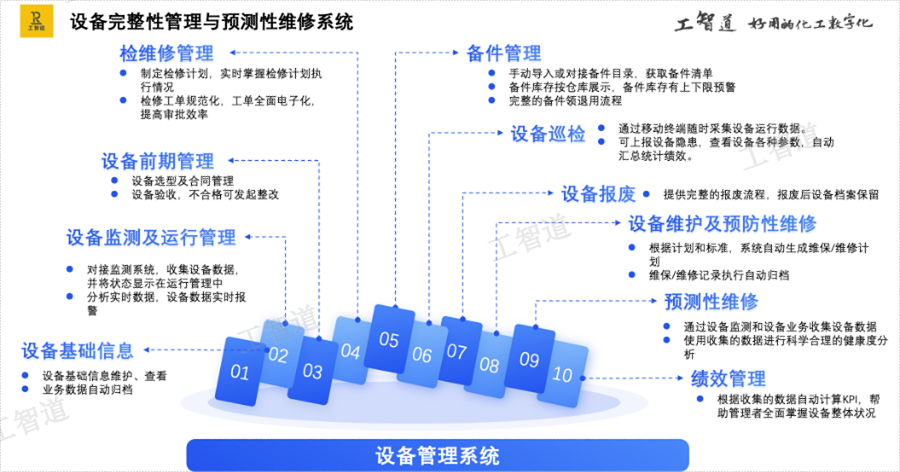
预测性维修系统涉及大量设备运行数据,数据安全保障至关重要。一方面,要防止数据泄露,采用加密技术对传输和存储的数据进行加密处理,确保数据在传输过程中和存储时不被窃取。例如,在工业互联网传输设备数据时,使用 SSL/TLS 加密协议。另一方面,要保障数据的完整性,防止数据被篡改。通过数据校验技术,如哈希算法,对数据进行校验,一旦数据被篡改,能够及时发现。同时,建立数据备份和恢复机制,定期对重要数据进行备份,并将备份数据存储在安全的位置。当数据出现丢失或损坏时,能够快速恢复数据,确保预测性维修系统的稳定运行和设备完整性管理的数据支持不受影响。
预测性维修系统需要处理来自不同传感器、不同类型的大量数据,多源数据融合技术在此发挥关键作用。例如,将设备的振动数据、温度数据、压力数据以及工艺参数数据等进行融合分析。单一的数据可能无法准确判断设备的故障,而多源数据融合后能够提供更的设备状态信息。通过数据融合算法,将不同类型的数据进行关联和整合,挖掘数据之间的潜在关系。比如,当设备振动异常时,结合温度和压力数据,可更准确地判断是由于机械故障还是工艺异常导致的。多源数据融合技术提高了设备故障预测的准确性和可靠性,为预测性维修提供更科学的依据,助力化工设备的完整性管理。通过预测性维修,企业可以提高设备的使用寿命。
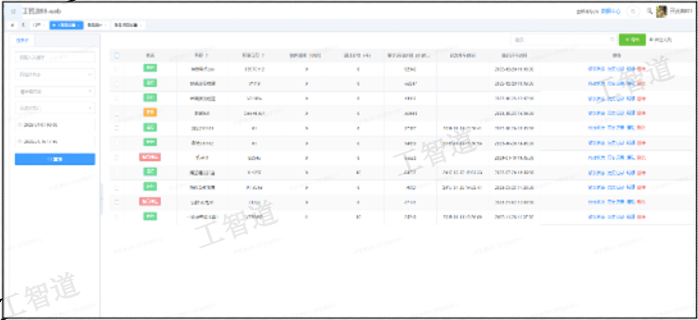
化工企业设备的运行优化是设备完整性管理的重要目标之一。通过深入且细致地对设备运行数据展开分析和挖掘,能够准确找出设备运行过程中的瓶颈和问题所在。比如,借助先进的数据分析算法,对设备运行的各项参数进行梳理,从而发现潜在的问题点。随后采取一系列有针对性的优化措施,提高设备的运行效率和产能。例如,运用智能算法优化设备的运行参数设置,使其达到良好工作状态;根据不同生产需求,灵活调整设备的运行模式;采用新型润滑材料和高效冷却技术,改善设备的润滑和冷却条件等。设备运行优化不仅能够提高生产效率,还能有效降低设备的能耗和磨损,延长设备的使用寿命,为企业节省大量的设备更新和维护成本 。化工行业对设备完整性的要求非常高。高兼容设备完整性管理与预测性维修系统技术规范
通过预测性维修,企业可以提高设备的运行稳定性。安全设备完整性管理与预测性维修系统维护记录
化工设备完整性管理需要建立完善的质量控制体系。从设备的原材料采购开始,对每一批次的原材料进行严格检验,确保其质量符合设计要求。例如,对于制造压力容器的钢材,要检验其化学成分、力学性能等指标。在设备制造过程中,设立多个质量控制点,对关键工序进行监督和检验,如焊接质量检验。采用无损检测技术,如超声波探伤、射线探伤等,检测焊缝内部是否存在缺陷。设备安装完成后,进行整体的质量验收,包括设备的安装精度、运行稳定性等方面的测试。在设备使用阶段,定期对设备进行质量抽检,如对管道进行壁厚检测,检查设备的腐蚀情况。通过这一系列的质量控制措施,确保设备在整个生命周期内都能保持良好的性能,保障设备的完整性。安全设备完整性管理与预测性维修系统维护记录
文章来源地址: http://swfw.chanpin818.com/rjkf/deta_26717034.html
免责声明: 本页面所展现的信息及其他相关推荐信息,均来源于其对应的用户,本网对此不承担任何保证责任。如涉及作品内容、 版权和其他问题,请及时与本网联系,我们将核实后进行删除,本网站对此声明具有最终解释权。