人为差错是制造过程中影响产品质量的重要因素。Q-TOP QMS系统通过整合质量管理六大工具和PDCA闭环管理,构建了系统化的人为差错防控体系,有效提升生产过程可靠性。 在Plan(计划)阶段,系统运用FMEA工具对关键工序进行失效模式分析。某电子制造企业通过Q-TOP系统的FMEA模块,识别出焊接工序的15个潜在人为失误点,并制定针对性防错措施。 在Do(执行)阶段,系统整合SPC和防错(Poka-Yoke)工具。实时监控关键参数的同时,在装配线设置智能检测工装。某汽车零部件企业应用后,操作失误导致的返工率从3.2%降至0.5%。 Check(检查)阶段,系统通过MSA(测量系统分析)确保检测可靠性。某 Act(改进)阶段,系统结合5Why分析和PDCA循环。 Q-TOP QMS系统还整合了控制计划(Control Plan)工具,将防错措施标准化。 该系统通过PDCA闭环管理,持续优化防错机制。未来,随着AI技术的深度融合,系统将实现更智能的人为差错预测与预防。质量管理系统提高设备效率。合肥半导体质量管理系统排行榜
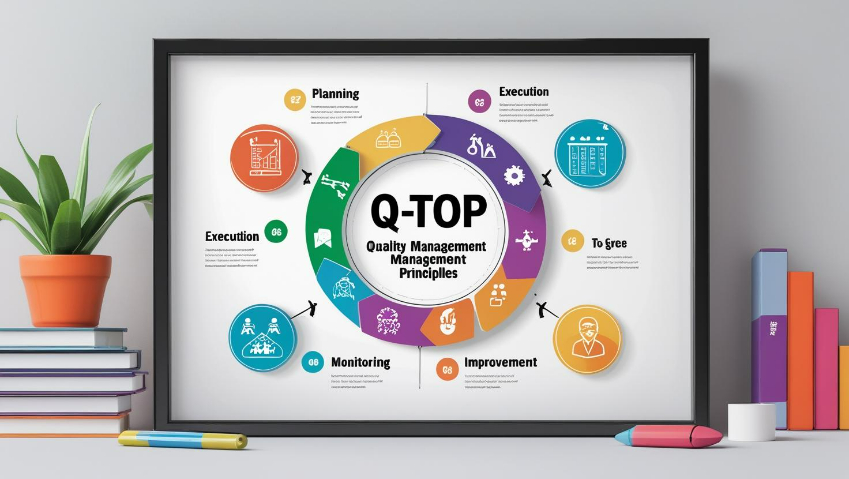
基于Q-TOP QMS系统的过程管控强化体系 过程管控能力是保障产品质量稳定的关键要素。Q-TOP QMS系统通过整合质量管理六大工具和PDCA循环管理,建立了全过程的质量管控体系。 在Plan(计划)阶段,系统运用APQP工具制定过程控制方案。某汽车零部件企业通过Q-TOP系统的APQP模块,对35个关键控制点建立管控标准,过程规范覆盖率提升至100%。同时结合FMEA识别关键过程风险。 在Do(执行)阶段,系统集成SPC和智能监控技术。某电子制造企业部署实时过程监控后,参数异常发现时间从4小时缩短至15分钟。自适应调节系统使关键工序CPK值稳定在1.67以上。 Check(检查)阶段,系统通过MSA确保过程数据准确性。某精密加工企业将测量系统波动控制在3%以内。系统自动生成过程能力分析报告,包含12项关键指标趋势。 Act(改进)阶段,系统结合5Why分析和标准化工具。某制药企业通过Q-TOP系统优化工艺参数后,批次间差异缩小70%。同时建立过程标准动态更新机制。苏州汽车电子质量管理系统价位质量管理系统稳定生产过程。
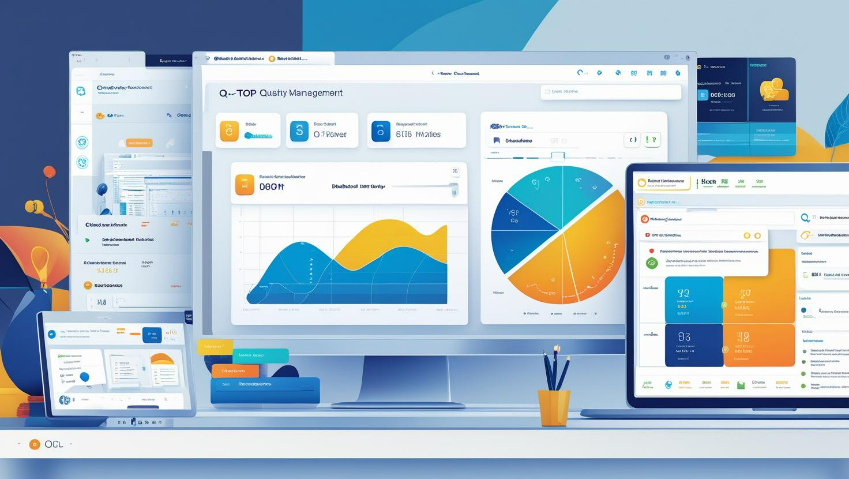
基于Q-TOP QMS系统的质量波动控制体系 质量波动的有效控制是企业实现稳定生产的关键环节。Q-TOP QMS系统通过整合质量管理六大工具和PDCA循环管理,构建了全过程的质量波动抑制机制。 在Plan(计划)阶段,系统运用FMEA工具识别波动源。某精密制造企业通过Q-TOP系统的FMEA模块,分析确定18个关键波动因素,并制定控制方案。同时结合APQP建立标准化作业体系。 在Do(执行)阶段,系统集成SPC和自适应调节技术。某汽车零部件企业部署实时监控后,关键参数波动幅度缩小65%。智能补偿系统使CPK值稳定在1.5以上。 Check(检查)阶段,系统通过MSA确保测量数据准确性。 Act(改进)阶段,系统结合5Why分析和标准化工具。 Q-TOP QMS系统还通过防错技术消除人为波动因素。 该系统通过PDCA闭环管理,实现了质量稳定性的持续提升。某新能源企业实施一年内,产品关键特性合格率从88%提升至99.2%,客户投诉下降55%。随着预测分析技术的应用,系统将为企业提供更准确的波动预警和更智能的调节方案。
产品研发效率的提升是企业保持技术先进优势的重要保障。Q-TOP QMS系统通过整合质量管理六大工具和PDCA循环管理,构建了高效的研发质量管理体系。 在Plan(计划)阶段,系统运用APQP工具规划研发质量路径。某新能源汽车企业通过Q-TOP系统的APQP模块,将产品开发周期缩短30%,同时确保各阶段质量达标。结合QFD工具将22项客户需求准确转化为技术规范。 在Do(执行)阶段,系统集成SPC和数字化样机技术。某智能设备制造商应用虚拟验证平台后,物理样机次数减少60%,研发成本降低45%。实时数据监控功能确保设计参数稳定性。 Check(检查)阶段,系统通过MSA保证测试数据可靠性。。 Act(改进)阶段,系统结合FMEA和知识管理工具。 Q-TOP QMS系统还通过防错技术预防设计缺陷。 该系统通过PDCA闭环管理,实现了研发质量和效率的同步提高。随着数字孪生技术的应用,系统将为企业研发提供更准确的虚拟验证和更高效的协同开发环境。质量管理系统降低质量成本。
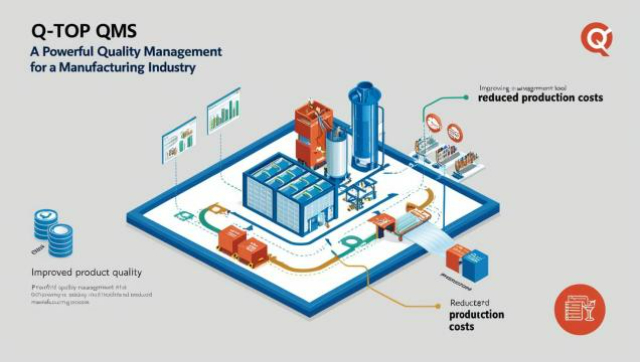
售后问题的有效预防是企业提升客户满意度的关键环节。Q-TOP QMS系统通过整合质量管理六大工具和PDCA循环管理,构建了贯穿产品全生命周期的售后问题防控体系。 在Plan(计划)阶段,系统运用FMEA工具开展售后问题预防分析。某家电企业通过Q-TOP系统的FMEA模块,识别出可能导致售后问题的28个关键风险点,并制定针对性预防措施。同时结合QFD工具将客户使用需求转化为设计规范。 在Do(执行)阶段,系统集成SPC和智能检测技术。某汽车零部件企业部署生产过程实时监控后,产品早期故障率降低65%。防错装置的应用使装配错误导致的售后问题减少90%。 Check(检查)阶段,系统通过MSA确保售后检测数据的可靠性。 Act(改进)阶段,系统结合8D报告和根本原因分析工具。 Q-TOP QMS系统还通过APQP工具在新品开发阶段预防售后问题。 该系统通过PDCA闭环管理,实现了售后问题的持续减少。随着大数据分析技术的深入应用,系统将为企业提供更准确的售后问题预测和更有效的预防方案。质量管理系统培养质量意识。苏州汽车电子质量管理系统价位
质量管理系统明确质量目标。合肥半导体质量管理系统排行榜
交付周期的有效缩短是企业提升市场竞争力的关键要素。Q-TOP QMS系统通过整合质量管理六大工具和PDCA循环管理,构建了高效的交付周期管控机制。 在Plan(计划)阶段,系统运用APQP工具优化生产流程。某汽车零部件企业通过Q-TOP系统的APQP模块,将产品开发周期缩短35%,同时识别出12个关键交付瓶颈点。结合QFD工具将交付时效要求转化为具体控制指标。 在Do(执行)阶段,系统集成SPC和智能排产技术。某电子制造企业部署实时进度监控后,异常响应时间缩短75%。自适应调度算法使设备利用率提升至92%。 Check(检查)阶段,系统通过MSA确保进度数据准确性。 Act(改进)阶段,系统结合5Why分析和标准化工具。 Q-TOP QMS系统还通过防错技术预防交付延误。 该系统通过PDCA闭环管理,实现了交付效能的持续提升。随着数字孪生技术的应用,系统将为企业提供更准确的交付预测和更智能的排产优化。合肥半导体质量管理系统排行榜
文章来源地址: http://swfw.chanpin818.com/rjkf/deta_28821697.html
免责声明: 本页面所展现的信息及其他相关推荐信息,均来源于其对应的用户,本网对此不承担任何保证责任。如涉及作品内容、 版权和其他问题,请及时与本网联系,我们将核实后进行删除,本网站对此声明具有最终解释权。